NVA Start-up Leverages Intellectual Property Developed at Auburn to Drive Space Exploration, Battlefield Logistics and the Internet of Things

NanoPrintek is leveraging Auburn’s world-renowned additive nanomanufacturing technology to create exciting new commercial and consumer market applications
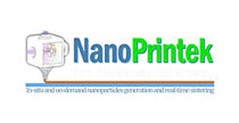
NanoPrintek, one of Auburn’s most exciting entrepreneurial teams and resident of the Auburn University New Venture Accelerator (NVA), is applying proprietary additive nanomanufacturing technology created in Auburn University’s Samuel Ginn College of Engineering to transform the way a wide range of electronics components and other next-generation materials and objects are designed and produced.
The company’s journey – from scientific breakthroughs, patent applications and prototype development to initial grant funding, technology licensing and expanding commercialization opportunities – exemplifies the tremendous potential of the intellectual property being developed at Auburn.
Their story is also a testament to the instrumental role Auburn’s Intellectual Property Exchange (IPX) plays in close collaboration with Auburn faculty, students and the NVA to help transform the potential of Auburn-based discoveries and inventions into powerful, real-world impact.
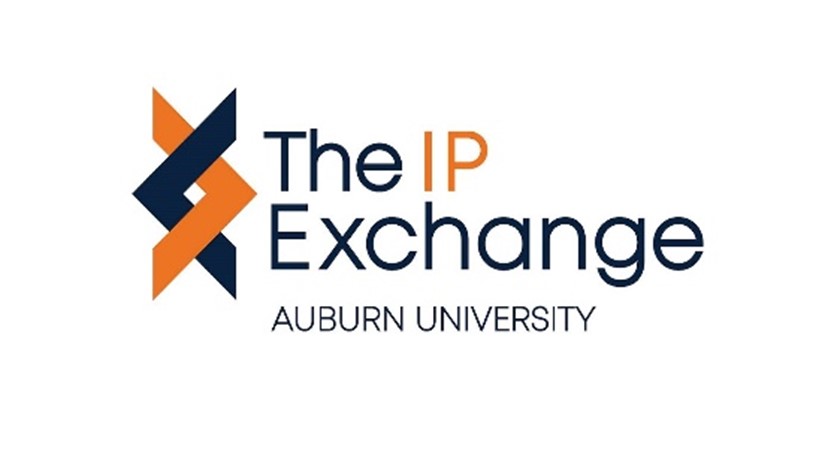
IPX offers Auburn researchers expertise and guidance regarding the protection of intellectual property – including patents and copyrights – and helps identify and secure licensing agreements with commercial entities.
The NanoPrintek Solution
NanoPrintek is taking a revolutionary approach to additive manufacturing that captures the benefits of an all-encompassing, laser-based, dry additive nanomanufacturing system design that enables the printing of electronics and other critical materials and products virtually anywhere, including in space.
“Our system is based on a fascinating technology that integrates all of the features, functionality and performance benefits of additive-for-electronics into a single, compact machine,” says NanoPrintek founder Masoud Mahjouri-Samani, assistant professor in electrical and computer engineering in Auburn’s Samuel Ginn College of Engineering. “The beauty of this system is that it can generate the nanoparticles required to manufacture electronic circuitry and other challenging devices from any solid material placed inside the machine – on demand and in real-time.”
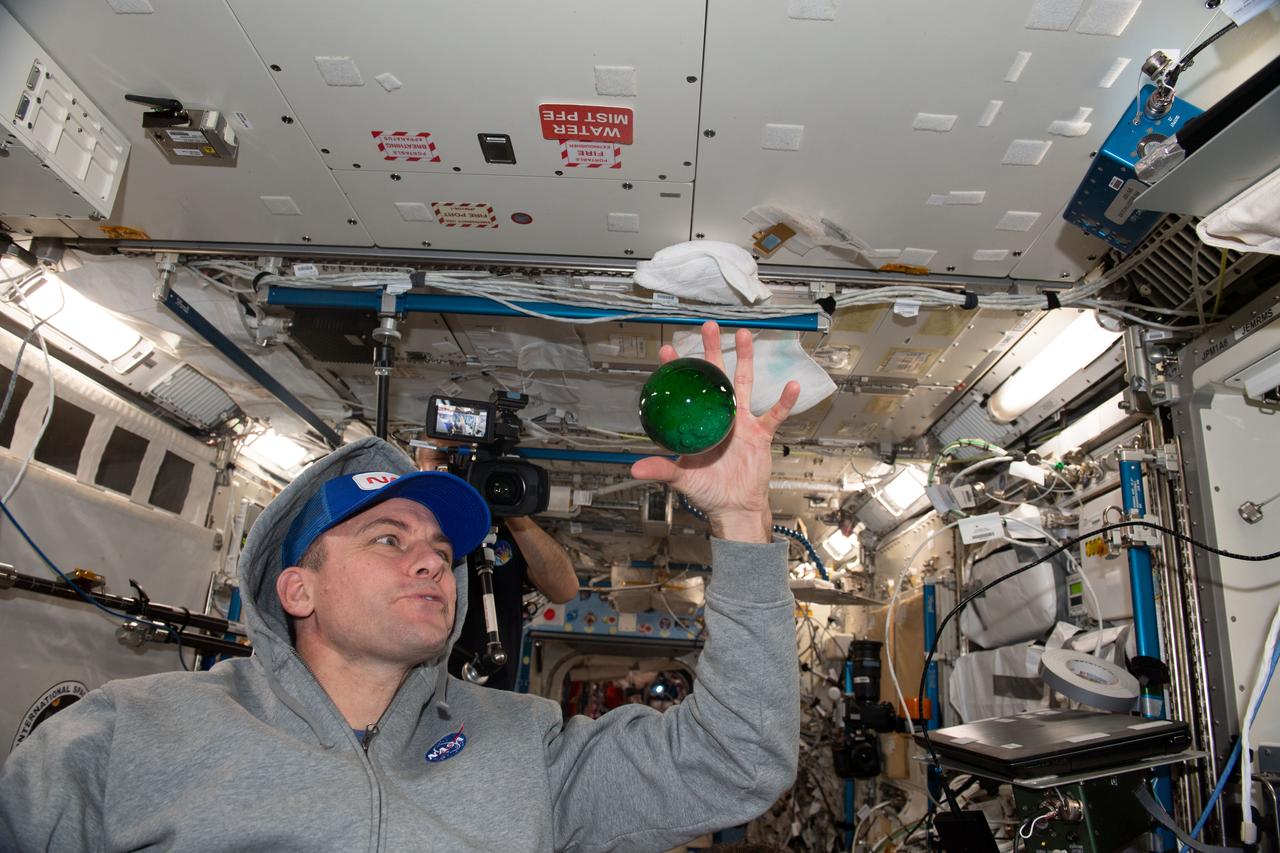
Expanding the Additive Universe
Auburn’s global reputation in advanced manufacturing – in particular, as a “Center of Excellence” for additive manufacturing research and development – is based primarily on an unparalleled expertise in creating parts that must not fail, complex physical structures for high-reliability applications such as fuel injection nozzles for GE Aviation’s jet engines. Auburn’s mission and its unique combination of additive manufacturing research and product commercialization expertise, however, extends well beyond these flagship applications to encompass an ever-broadening array of products and markets.
That’s where NanoPrintek comes in.
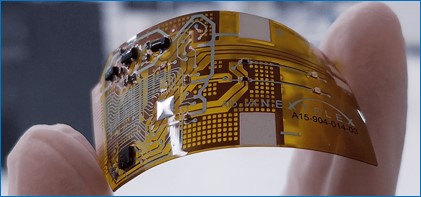
NanoPrintek has developed a groundbreaking system that brings an innovative technological approach to entirely new segments of the additive manufacturing application spectrum.
Masoud explains why his team’s new additive manufacturing technology means so much to this emerging industry and how Auburn’s leadership is changing the way electronics and other critical components are designed and integrated into commercial and consumer-focused products – some of which have yet to be imagined.
‘Traditional’ Additive Systems
“We are all aware that ‘normal’ additive manufacturing is changing the way we design and develop structural parts – that’s been our collective focus to date,” says Masoud. “In these applications, we utilize different types of large, complex additive manufacturing machines, some using a powdered bed and jet where powder is blown and then lasers start sintering the particles together. Others use liquids or aerosols to target different types of materials for structural product manufacturing.”
“These systems are designed to produce a relatively small quantity of high-value structural parts” notes Masoud, “and they perform phenomenally well in these critical applications. But when you try to apply traditional additive manufacturing to producing electronics and functional devices, everything changes. We’re dealing with much smaller device geometries and we’re also dealing with desired functionalities.”
Masoud also points out that structural parts-focused additive manufacturing systems require large facilities, expensive and hard-to-procure materials, and complex supply chains that just won’t work in additive-for-electronics.
“Today, the main additive systems for electronics are based on inks – and that’s extremely expensive and it takes a long time to formulate them,” says Masoud. “In the past 10 years, for example, more than 90% of the printing inks have been silver, and we can’t even readily print sensitive materials such as pure copper, superconductors, or semiconductors. The ink formulation requires solvents, polymers, and binders, and as soon as you add these extra elements, you’ve contaminated the process. That’s unacceptable, especially for electronics and functional devices.”
Another limitation to liquid ink- and aerosol-based systems for electronics is that you’d need multiple manufacturing facilities and a complex supply chain to even try to make an ink-based approach work. “You’d have to first make the nanopowders in a powder manufacturing facility, then it goes to another facility or company to make the ink for a given application with specific viscosity criteria and other critical characteristics. Then, after printing, they should be post-processed to sinter the line and remove the added solvents and polymers – many of which are contaminative and pollutive materials. Add to that the fact that the useful lifetime of those inks is very short, meaning they must be used quickly and disposed of properly.”
“Because of these complexities, it is literally impossible to find materials and systems capable of printing multimaterial and multifunctional electronic circuitry needed via traditional additive manufacturing methods.”
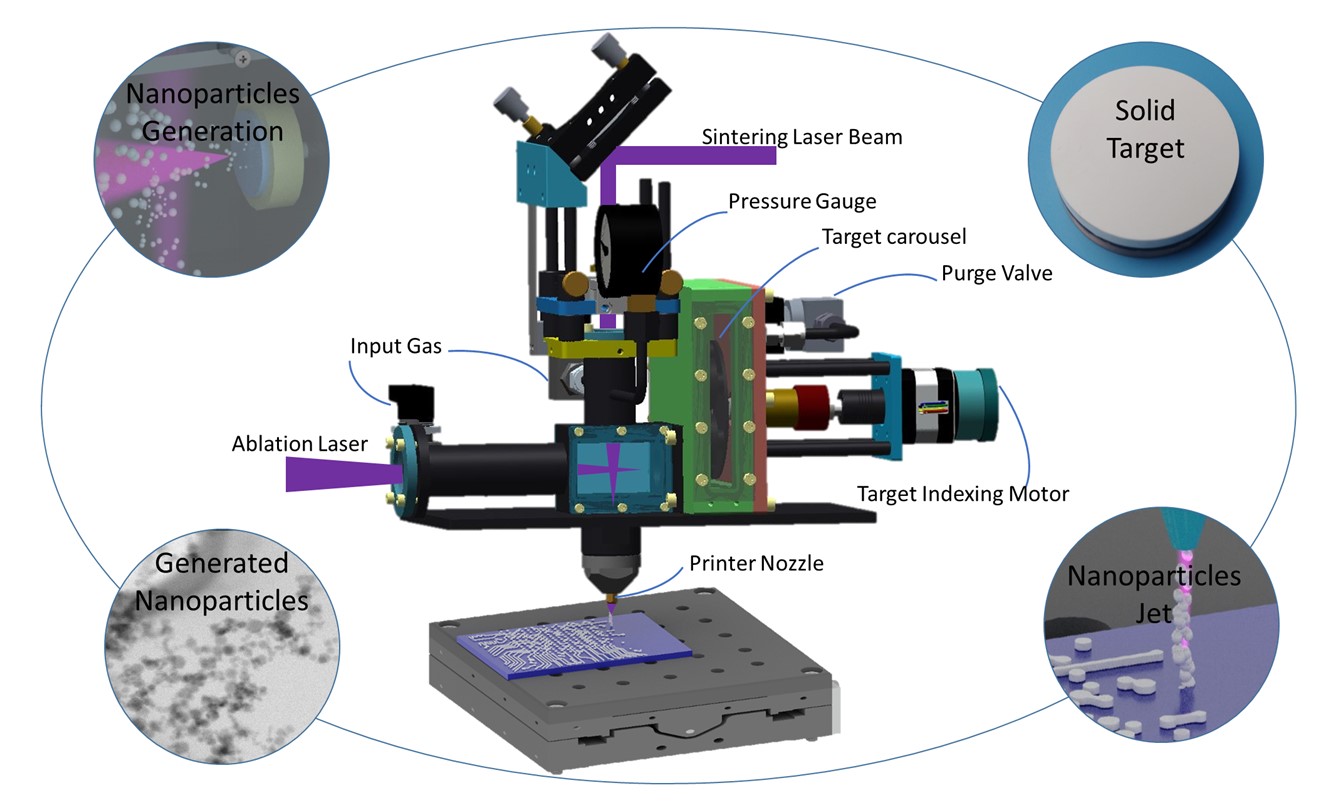
Taking Additive to the Next Level
These differences are important as we explore and progress the development of high-precision manufacturing into outer space while also helping drive the Internet of Things, (IoT) where an explosion of promising connectivity capabilities is poised to deliver extraordinary value to our lives. To make all this happen, Masoud urges the additive manufacturing industry and its current and potential customers to join him and his company in developing innovative ways to embed electronic functionality into a wide and varied range of surfaces, materials, and applications.
“In the near future, we need to make everything smart – including ‘normal’ objects,” notes Masoud. “We need to embed intelligence into literally billions of these formerly inert, unconnected products, materials, and places. We need them to be able to identify, collect and compile specific data, process them, and then contribute the value of that curated data to a network of other objects and systems across the globe.”
Driving Creativity at Both Ends of the Additive Spectrum
The NanoPrintek team’s research demonstrates that their developed integrated system can generate a jet of dry nanoparticles on demand. When these nanoparticles are directed toward a substrate, they can be sintered in real-time to form the desired electronic circuits or physical parts.
The value of this extraordinary capability extends beyond foundational applications all the way into space-based manufacturing research. All you have to do is look at Apollo 13, where the astronauts on-board their crippled spacecraft were forced to cobble together a CO2 filtration system out of boxes and bags to stay alive. Imagine if the broken part were an electronic circuit or a small physical component that couldn’t be made with any combination of things already on board the spacecraft. Looking ahead, how can we equip astronauts with the ability to create electronic circuitry and other critical parts they may need to repair what may fail in space?
NanoPrintek’s system is designed to be able to do just that, and their work has already garnered robust interest and funding from NASA targeting the creation of viable methods for manufacturing functional devices in space via the team’s dry printing technology – including circuitry.
Here on earth, the ability to quickly produce spare parts on the battlefield or in natural disaster zones could also offer military and first responders uniquely valuable alternatives to challenging and vital spare parts supply chains.
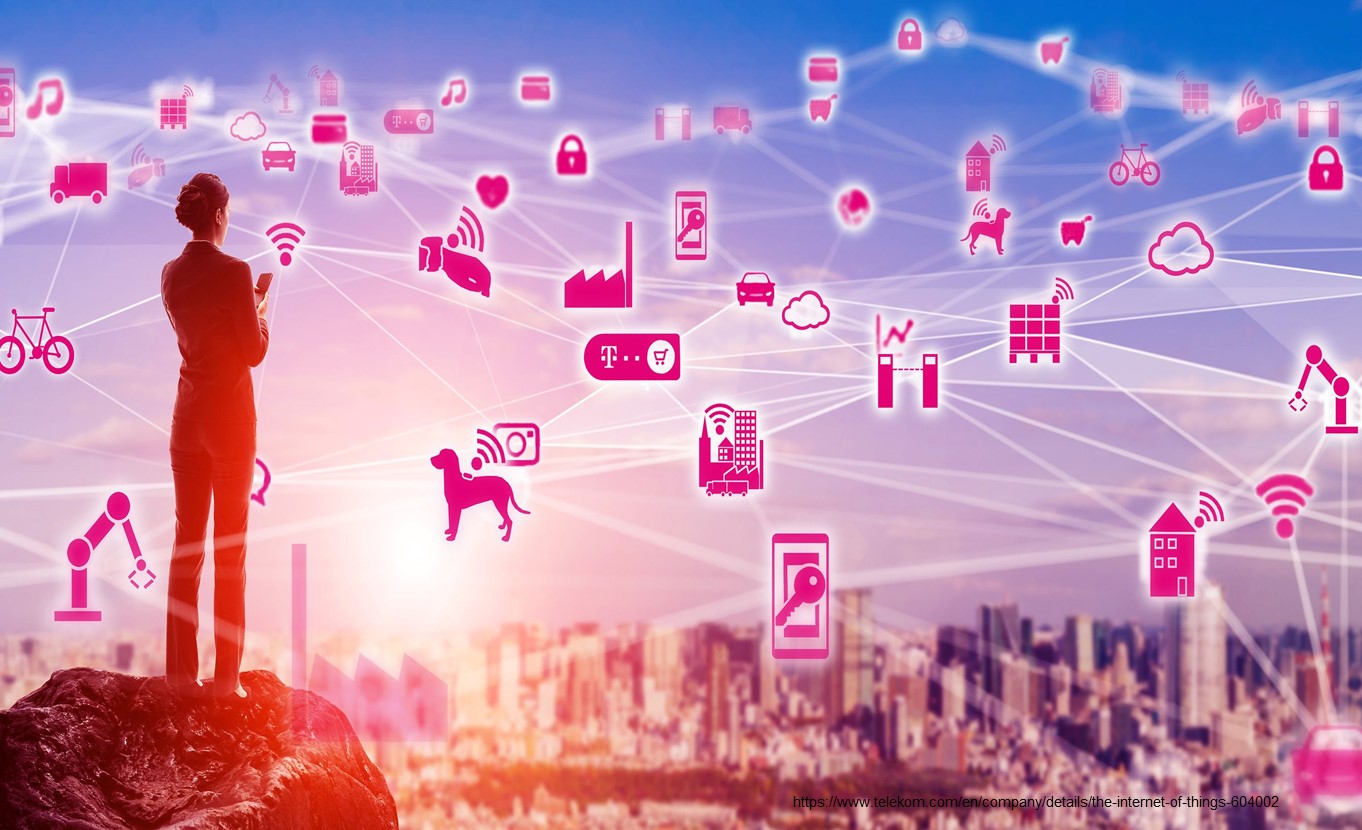
Building the IoT
At the other end of the additive application spectrum – designing and producing custom electronics for a wealth of emerging consumer products that will comprise the IoT – NanoPrintek solves a different set of challenges.
“To make the IoT happen, we need to integrate various electronic functionalities into a wide variety of objects that have different shapes. You want to have antennas, sensors, capacitors, batteries, chips, etc. – all printed onto or integrated into these objects.
It’s not like manufacturing complex microprocessors or circuits for cell phones or laptops, for example, where once a design is set and sent to a fab where these standard components are pumped out in high volumes.” Masoud also points out that these complex electronics typically take between six months to two years from initial design to when they finally come to market. If you make a mistake along the way, you have to go repeat the whole process. That simply doesn’t fit a market like the IoT, in which eventually billions of different objects and customized electronics will be required for each.
“Our approach is so much cheaper and so much faster. You can go from design to test in one day. It requires much less energy and production can be distributed – not centralized in multi-billion-dollar facilities. You can begin with a handful of our compact systems and ramp production as demand warrants simply by adding additional machines.”
This efficient, economical, and extremely flexible system design also opens up this emerging market to a virtually unlimited number, size, and type of new companies – including small businesses, the backbone of innovation and entrepreneurship. This is, perhaps, the most exciting aspect of the tremendous value NanoPrintek brings to the growth of additive manufacturing.
The Door is Open
“We want to put our machines into the hands of talented engineers, designers, and others working to make the IoT and other new markets a reality. The fact is, we don’t even know all the places the revolutionary capabilities of our system will end up opening doors to the creation of innovative applications we haven’t imagined yet. The possibilities are literally unlimited.”
To learn more about how NanoPrintek can help make your idea, innovation, or new product design a reality, please visit https://nanoprintek.com/ or contact Masoud at mns19@nanoprintek.com.
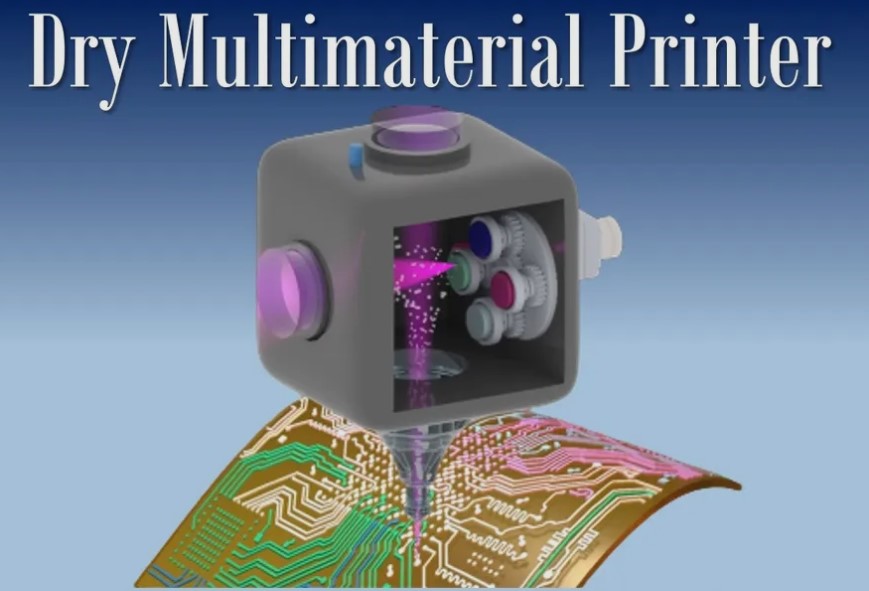